Drilling Mechanics Group
With increasing challenges in drilling for minerals, hydrocarbon and geothermal exploration, a new scientific group dedicated to drilling mechanics was established in 2010.
The research interests of the Drilling Mechanics Group (DMG) centred around the interactions taking place while drilling: interactions often coupled between the drill bit, the rock, the drilling fluid and the driving mechanisms (drill rig, downhole motors). Scientific research is conducted with the overarching objective of delivering simple, practical engineering models but also technical solutions that can be implemented on site.
The DMG has established active collaborations with industrial partners with the objectives of implementing results of research to optimize drilling performance via the design and selection of tools, the implementation of best drilling practices and the monitoring and interpretation of drilling data in real time.
Research interests
Understanding the process of fragmentation and frictional contact, but also the process of wear or damage mobilised at the interface between the rock and the bit is an essential step towards improving drilling performance. The DMG laboratory consists of four tailored designed state of the art drilling rigs designed to study the interaction between various types of rotary bits (PDC, roller cone or diamond bits) and sedimentary or crystalline rocks.
Experiments conducted under servo-control and with precise measurement provide insights on (i) the nature of the various mechanisms that control the relation between the forces (thrust and torque) acting on the tool and the velocities (rate of penetration and angular velocity) for a given state of tool wear, fluid properties and rock mechanical properties and (ii) the processes that control the relation between operating parameters, rock, fluid properties and wear rate.
By developing models and in turn methodologies to interpret the effect of operating parameters, drilling fluid, bit or rock properties from the drilling response, it opens opportunities to develop an interpretation scheme to infer from the drilling data not only a diagnosis of the performance (bit state of wear, bit cleaning) but also rock mechanical properties.
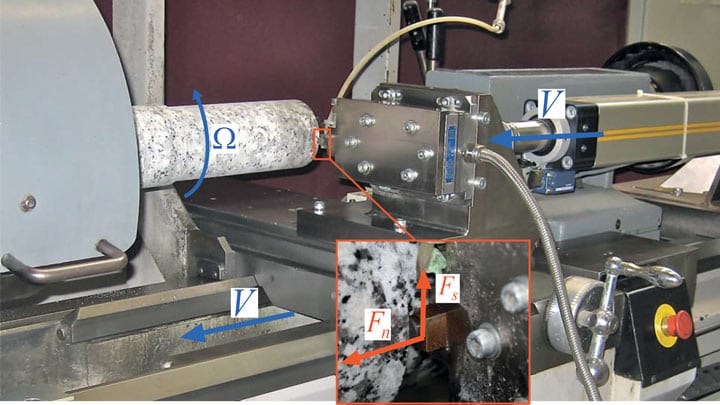
Thor: Laboratory drilling rig to study cutting action and wear of PDC and impregnated diamond bits
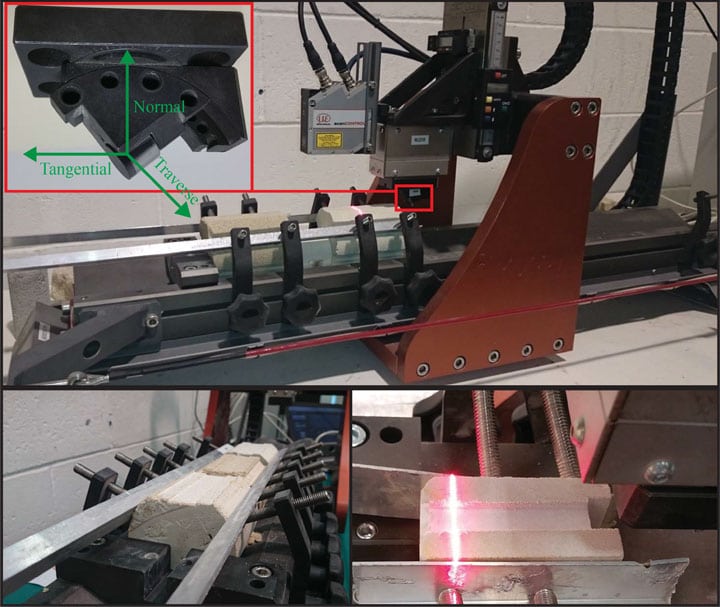
Wombat scratch test: The rig used to study the cutting action of PDC cutters
One avenue to improve productivity in diamond drilling is to operate at high angular velocities. However, there are numerous challenges associated with bit wear, erosion, hole cleaning, and vibrations. The DMG research interest is to develop different fluid, bit material/designs to test in conjunction with different downhole motors to tackle these challenges paving the way for faster and cheaper drilling operation.
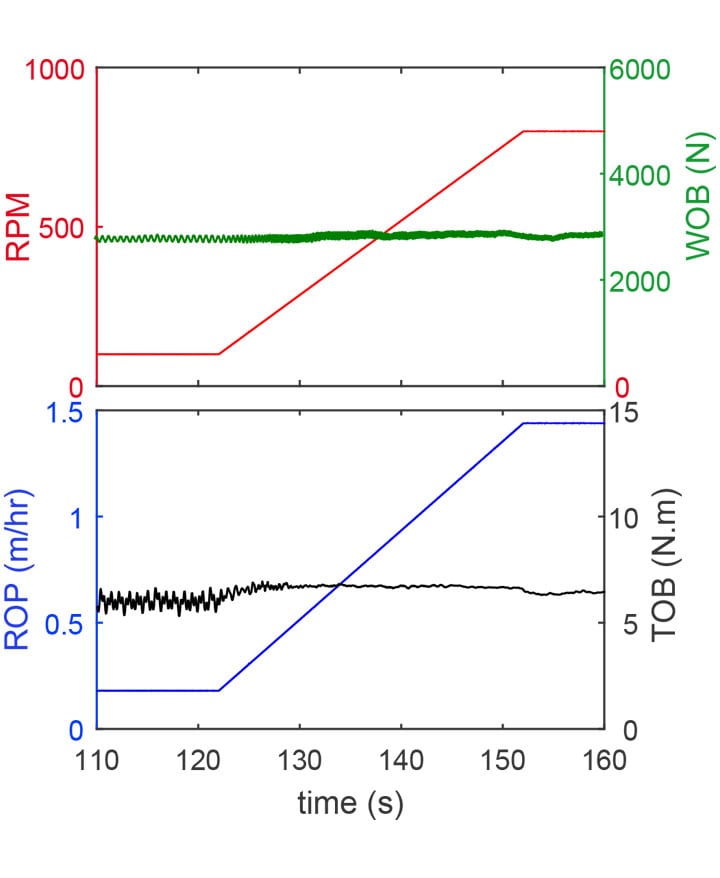
Example of improvement in productivity at high speed drilling: ROP increases by RPM at the imposed weight on bit.
One of the research interests of the DMG is drilling fluid. The group has developed a state of the art flow loop system equipped with various sensors including high speed video camera to characterise and improve various drilling fluid functionalities including hydraulics, hole cleaning, fluid loss and wellbore stability and solid removal. Field trials took place in South Australia and Victoria looking at both the designs of fluid, and also at the implementation of drilling practices and a methodology to monitor and interpret data in real time on the site. Successful results have led to patenting a novel recipe for a drilling fluid targeting fluid loss and borehole stability.
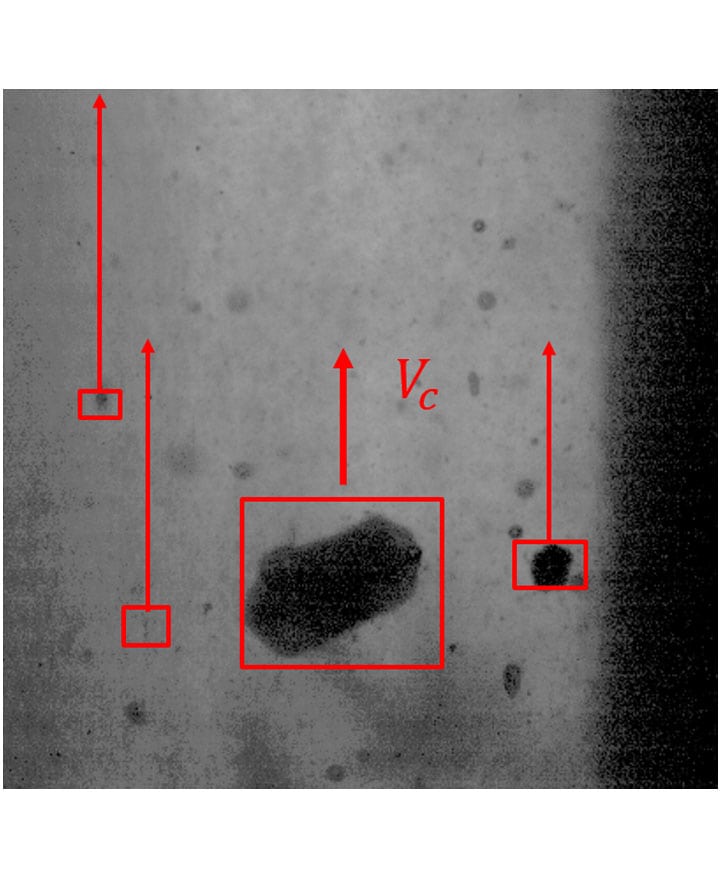
Measurement of cuttings velocity using a high speed video camera
The DMG is currently designing a large laboratory equipment to be able to run full scale drilling experiment with a variety of driving system, in particular hammer (air or water) and high speed motors or turbines.