New crane device will make worksites safer
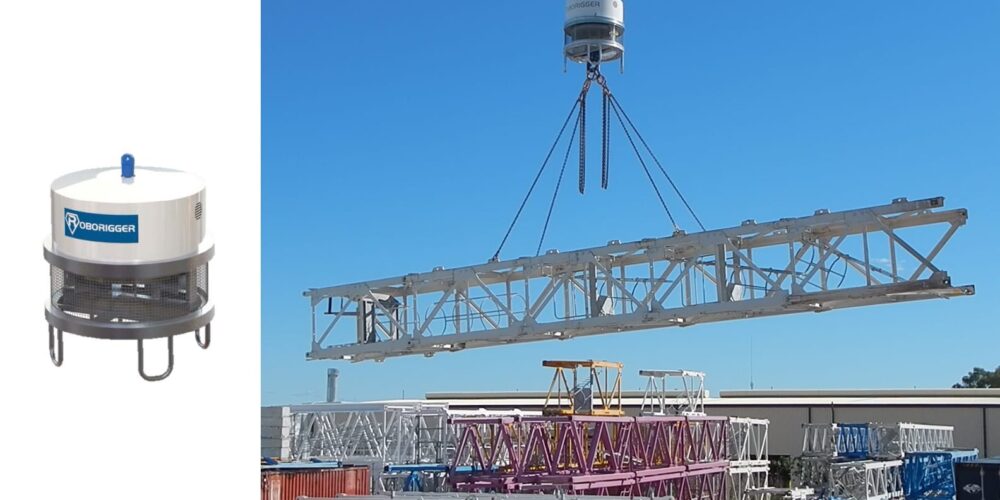
Curtin University researchers have been working with engineering solutions provider TENSA Equipment to develop a control algorithm for TENSA’s new wireless rotation device, which will drastically improve worksite safety by allowing riggers to orient loads from a safe distance.
The Roborigger, which is hooked on to the end of a crane, can position and orient crane loads by remote control using gyroscopic and inertial forces.
It is battery powered, with the capability to operate for at least 12 hours between charges and includes a load cell and camera. It is controlled and monitored with a wireless remote with a minimum range of 100 metres, removing the need for workers to be in the vicinity.
Other key features include the ability to release loads remotely, and inbuilt safeguards and fail-safe protection to prevent an unwanted release.
Most construction and oil and gas companies currently employ riggers who position and orient crane loads using ropes and by manually pushing or pulling. The task requires riggers to stand in proximity to the loads, putting them at potential risk of injury or death if accidents occur.
The risks were exposed last month, when one man was killed and two injured after 1.5 tonnes of concrete fell from a tower crane at a Melbourne construction site.
Controlling Roborigger
For safe operations, Roborigger had to be designed to maintain stability when autonomously rotating crane loads in the presence of unpredictable disturbances, such as wind.
To accomplish this, TENSA Equipment sought help from Curtin to develop a mathematical algorithm for determining the appropriate amount of torque needed by Roborigger’s motor under different conditions. This work was supported by almost $30,000 in grant funding from Innovation Connections, a government scheme that pairs small-to-medium businesses with research institutions to work on a new product or service.
Dr Fabrizio Padula, an expert in control systems from Curtin’s Faculty of Science and Engineering, worked on the task in collaboration with his Curtin colleagues Professor Ryan Loxton and Associate Professor Lorenzo Ntogramatzidis.
“Control algorithms are pieces of technology that are hidden. They are everywhere: in cruise control, in flight control and in mobile devices,” explains Padula.
“For Roborigger, we first built a mathematical model of the machine. Then, based on that model, we designed an optimal torque signal, which uses data readings from sensors that measure the Roborigger’s orientation and speed.”
The primary challenge that the researchers had to overcome was the absence of data sensors on the load itself.
“The sensors measure Roborigger’s speed and orientation, but not the speed and orientation of the crane load. So, we need to control the behaviour of something we cannot measure,” says Loxton.
“The goal was to ensure the Roborigger could quickly move to the final orientation and also adjust for unpredictable external disturbances, guaranteeing stability so that the load does not spin wildly. The final control algorithm can do this.”
Adds Padula: “Normally, companies must stop lifting when it’s windy, but because the Roborigger always keeps the load under control, it can operate in stronger winds and other dangerous environments, so both productivity and safety are improved.”
Product rollout
After a month of successful full-time testing, TENSA Equipment is now making final preparations to operate the Roborigger on a major construction site in the Perth central business district.
“Curtin’s assistance on this project has been invaluable,” says TENSA Equipment Managing Director Derick Markwell.
“Multiplex and Woodside have been supporting us and both companies are now very keen to use it on their sites. We also have a long list of other companies that want to trial it so we are very optimistic about the commercial viability of this product.”
According to Markwell, Curtin’s input and the experience of testing the Roborigger directly with the crane operators resulted in a simpler and more robust solution for the device’s control and functionality.
“Initially, we implemented fully automated repositioning, yet the riggers preferred to use a more manual control method even though it requires a little bit of practice,” he says.
“This allows the unit to work a lot more efficiently and we ended up with a much better solution.”
“It’s important to have good mathematics, but the riggers need to be comfortable using the technology. They have to trust how the machine feels,” Padula notes.