Getting dirty to clean up the chemical industry’s environmental impact
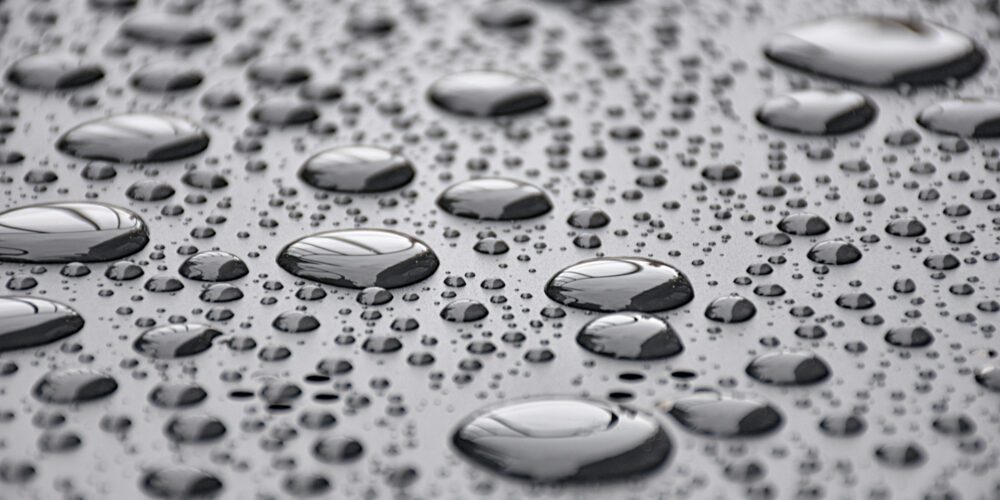
The global chemical industry is a major fossil fuel consumer and climate change contributor; however, new Curtin University research has identified how the sector could clean up its green credentials by getting dirty.
Most chemical reactions involving electricity and organic materials can’t be done efficiently using water because the organic materials don’t dissolve well, forcing industry to use fossil fuels to provide heat rather than electricity or use alternative substances to water, which add environmental and safety risks.
However, a team of researchers led by Associate Professor Simone Ciampi, from Curtin’s School of Molecular and Life Sciences, has found chemical reactions in water can be dramatically sped up by adding a water-resistant material to an electrode – a process known as “fouling”.
“Fouling goes completely against conventional wisdom, which says you have to have clean instruments to make processes using an electrode as efficient as possible,” Professor Ciampi said.
“But when we’ve added water-resistant materials such as plastic or oil, we’ve found reactions happen in these areas up to six times faster than in the “clean” areas of the electrode.
“We found even using a household glue improved reaction speed by 22 per cent.”
Study co-lead and PhD candidate Harry Rodriguez said the key was the organic material being attracted to other water-resistant materials.
“If the material is hydrophobic – which means it doesn’t like water – it will want to get out, so it will be drawn to a hydrophobic environment such as oil, plastic or glue on an electrode,” he said.
Mr Rodriguez said the chemical industry was eager to use water where possible, despite the challenges.
“If organic chemicals were to be manufactured in water using current industrial methods, the yield is expected to be very poor,” he said.
“But companies still want to use water if it’s viable, because the chemicals they currently use for these reactions are expensive and flammable, so there are concerns and potential complications over safety and storage.
“As well as the environmental benefits, using water bypasses a lot of those issues.”
Professor Ciampi said it would be some time before the method was replicable at a large scale, but the journey towards a cleaner chemical industry could be accelerated by collaborating with other areas of expertise.
“For example, the mining industry uses bubbles as a way to separate minerals all the time,” he said.
“There’s a wealth of knowledge out there which could be paired with electrochemistry to bring this method up to a bigger scale and then have a real impact.”
‘Insulator-on-Conductor Fouling Amplifies Aqueous Electrolysis Rates’ was published in the Journal of the American Chemical Society.